Technical Data
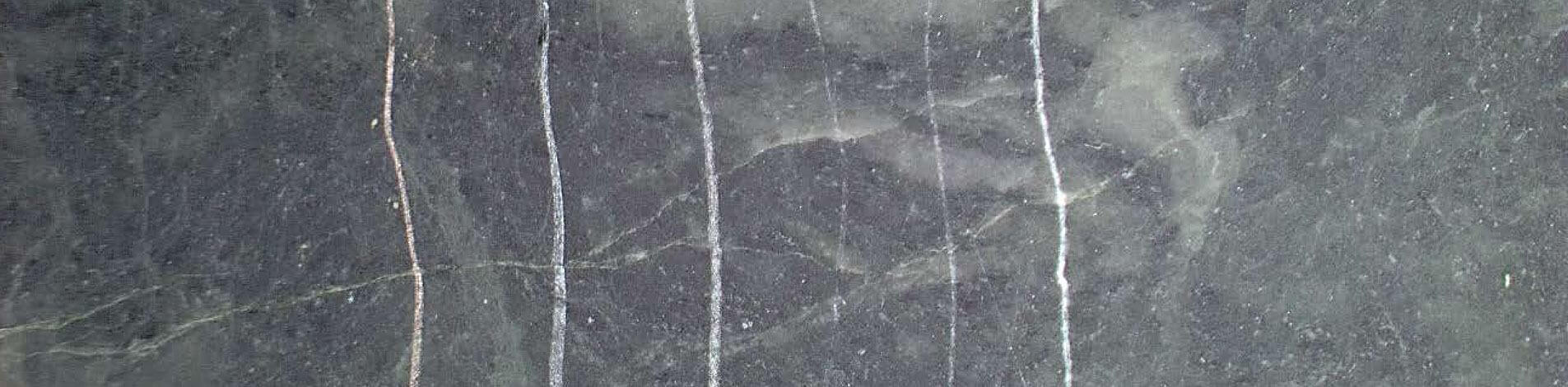
Commitment to Excellence
There are many factors that play a role in creating the specialty aggregates, natural thin stone veneer, and other products that Kafka Granite manufactures. Our decades of experience in the industry have made it clear to us that architects, designers, stonemasons, and others need high-quality specialty aggregates and masonry units that will hold up under stress and against natural forces. Kafka performs various testing methods on their materials to ensure the product is suited to your project specifications. To further demonstrate our commitment to transparency and quality, all test data is available to our customers.
When you purchase specialty aggregates and other natural stone products from Kafka Granite, you can rest easy knowing the materials you receive will be of the highest quality.
Specific Gravity
Kafka Granite adheres to ASTM material specifications for our stone products. Samples of our specialty aggregates are sent out for a number of tests, including ASTM C127: Standard Test Method for Specific Gravity and Absorption of Coarse Aggregate. This particular assessment determines the density of a given aggregate. This data can help determine whether the crushed stone is appropriate for a specific application.
Read MoreAbsorption
ASTM C127 also determines the absorption of a given aggregate. Different absorption levels determine how well a specific type of stone will withstand weathering and structural stress, and, by extension, how a product can be used. It’s essential that the qualities of a stone match the needs of the application. Absorption capacity is particularly important in natural stone products that will be exposed to the elements and undergo the freeze-thaw cycle.
Read MoreMohs Hardness
The Mohs scale of mineral hardness is used to measure the scratch resistance of a material, and also aid in identifying minerals. Measurements range from 1 to 10, with 1 indicating the softest material and 10 the hardest. Depending on what the aggregate is being used for, there may be an industry specification or product standard that states how hard the stone needs to be. For example, an abrasive quality allows harder stone products to stand up to harsh environments, or allows softer stone products to polish more effectively.
Read MoreSieve Analysis
The process of a sieve analysis is used to determine an aggregate’s gradation, or the distribution of stone particles by size, within a given sample. The sieve analysis is especially important to evaluate the performance of aggregates for their intended uses, and can be critical in the strength of the finished product, compaction of the aggregate, or the visual aesthetic. A sieve analysis is also helpful as a measure of quality control and consistency when crushing. Kafka produces a large range of aggregate sizes to meet nearly any size specification.
Read More