No two pieces of natural stone look alike—even if you’re comparing two pieces of granite extracted from the same quarry. This variation of color, pattern, and texture is part of what makes natural stone so unique and so highly prized as a building and landscaping material. If you’re on the lookout, you’ll notice it in…
Read More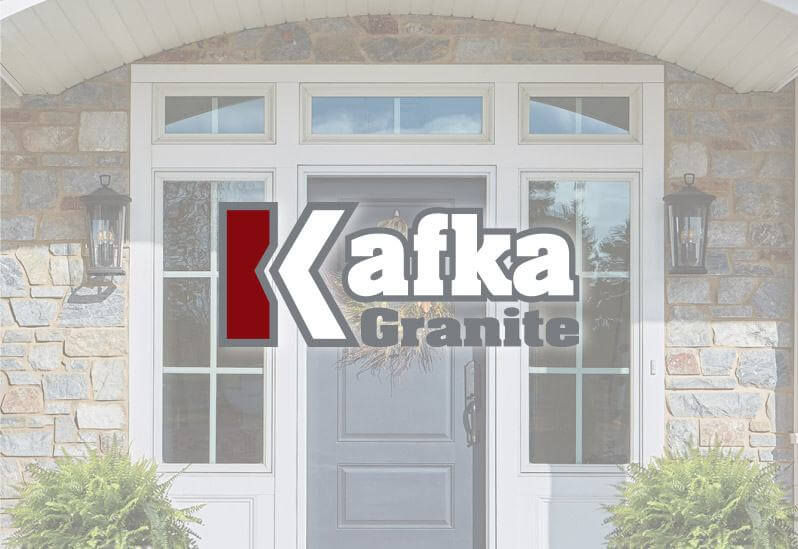